Traditional wired Ethernet and Wi-Fi networks frequently fail to meet the needs of modern and mobile autonomous systems due to constraints in widespread coverage, bandwidth, latency, and scalability. Private 5G networks can be a critical resource for attaining unprecedented operational efficiency, such as reducing downtime and improving productivity through reliable connectivity for automated systems and IoT devices.
Why private 5G for manufacturing?
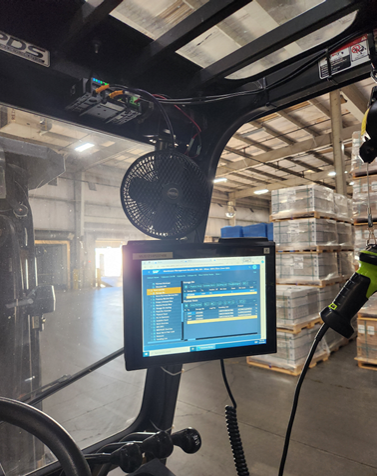
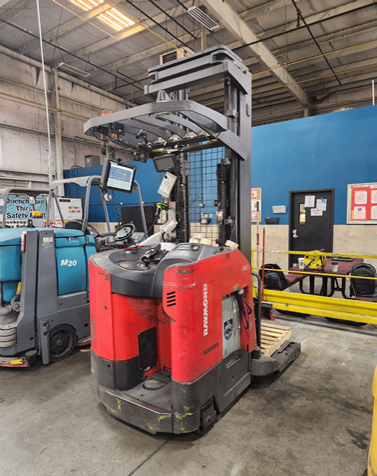
- Wider and more reliable coverage across complex indoor and outdoor spaces, with much broader range, more resilient connectivity, deeper security per use case, etc. With a range of several kilometers per cell—far exceeding Wi-Fi—it ensures seamless, low-latency connectivity for AGVs, robotics, and IoT. Network slicing and encryption enhance security per use case, while ultra-reliable handovers reduce downtime. For example, manufacturers have reported up to 30% gains in operational efficiency with private 5G.
Productivity Gains:
- +42% equipment productivity, +41% worker productivity with 5G (Manufacturing Institute).
- Up to 30% improvement by reducing downtime and optimizing operations (ABI Research).
Cost Reductions:
- Energy savings in manufacturing up to 20%, maintenance costs down 25–30% through predictive maintenance (ABI Research).
- Up to 30% improvement by reducing downtime and optimizing operations (ABI Research).
- High-speed, low-latency connections that Wi-Fi struggles to maintain in industrial settings. For instance, Wi-Fi networks may saturate with as few as 5 to 10 devices per access point, necessitating multiple networks to accommodate all devices. (automate.org)
- Dynamic and mobile connectivity needed for modern automation, robotic and IoT initiatives in diverse industrial environments – something Wi-Fi cannot properly support with its fixed configuration needs.
Private 5G for manufacturing: Highway 9 Mobile Cloud
Highway 9 Mobile Cloud delivers private 5G for manufacturing environments with outstanding range, security, and reliability. With an integrated cellular services stack that streamlines deployment and tight integration with existing IT network / security infrastructure and major carriers, the Highway 9 Mobile Cloud offers a transformative approach to deploying and operating private mobile networks.
Highway 9 Mobile Cloud offers a significant shift when it comes to the operation of smart factories and most importantly, addresses the critical need for reliable and far-reaching connectivity. As Industry 4.0 continues to evolve, Highway 9 Mobile Cloud helps future-proof industrial enterprises against the complexities of modern manufacturing. Embrace the power of connectivity and embark on a transformative journey that will redefine your factory’s potential and pave the way for sustained success in the digital age.
The Highway 9 Mobile Cloud has already proven its transformative power in real-world applications. Let’s explore how it helped a leading tile manufacturer overcome its connectivity challenges
Case Study: Private 5G for a leading tile manufacturer
A leading manufacturer and distributor of ceramic, porcelain, and stone tiles operates a large-scale production and distribution facility. The existing network infrastructure was insufficient to meet the demands of IoT deployments, automation and complex logistics, leading to inefficiencies and connectivity challenges within the warehouse. The facility, which served as a central hub for manufacturing and distribution, relying on Wi-Fi networks faced several critical challenges related to connectivity and operational inefficiencies
Some of the specific challenges faced included—
Reliable Mobility in Challenging Environments- Wi-Fi connectivity drops in outdoor and RF-dense areas led to operational inefficiencies.
- Private 5G provided seamless coverage across warehouses, factories, and open yards.
- Wi-Fi struggled with latency spikes impacting real-time control of AGVs, forklifts, and robots.
- Private 5G delivered consistent latency, ensuring smooth autonomous operations.
Scalability for Industry 4.0
- Increasing automation, AI, and robotics required a future-proof network.
- Private 5G supports massive IoT deployments and 5x more connected devices vs. Wi-Fi
The company partnered with Highway 9 to create a private cellular network tailored to its facility’s needs. Highway 9 deployed a secure, private 5G-enabled Mobile Cloud exclusively for the company, eliminating interference from public networks and ensuring reliable connectivity. This scalable infrastructure has enabled the company to embrace automation and IoT technologies, improving operational efficiency and supporting long-term goals.